Computer vision in oil and gas serves as a pivotal artificial intelligence (AI) technology adopted by a majority of companies in the sector. Within the oil and gas industry, computer vision presents substantial opportunities for advancement and expansion, transforming operational processes. Organizations strive to generate value through AI solutions rather than depending solely on conventional, human-based methods.
As artificial intelligence reshapes the industry, companies develop in-house expertise, design custom AI vision solutions, and gain insights through early implementation and refinement of AI systems on a large scale. Let’s examine the top 12 applications for oil and gas computer vision.
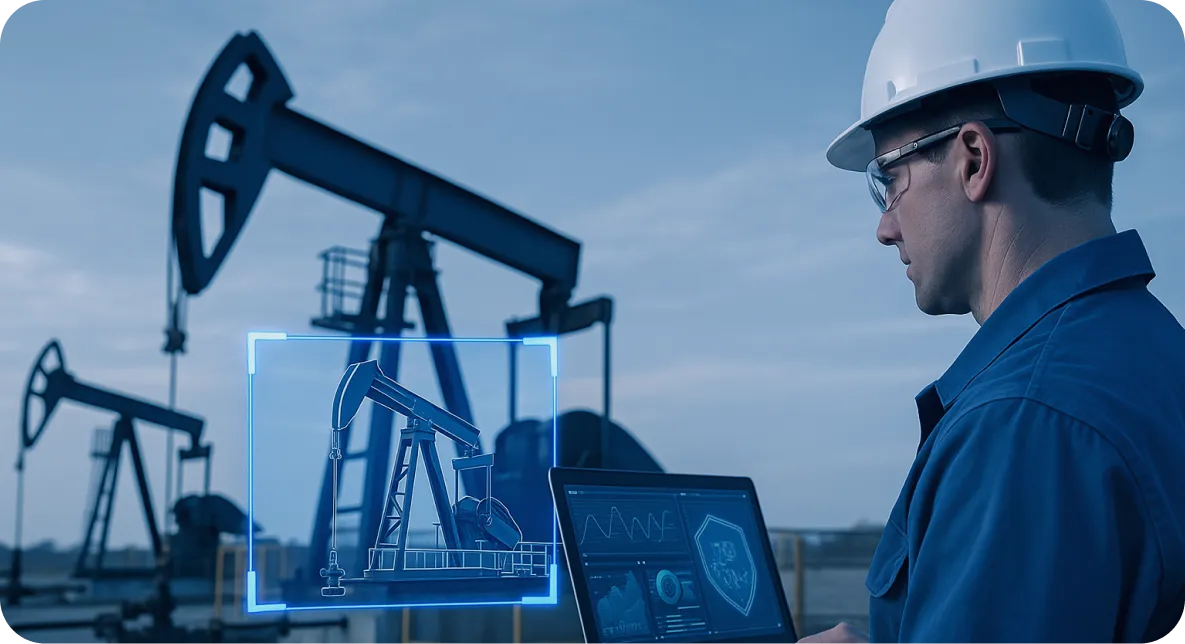
1. Automated Reading of Analog Instruments
Computer vision interprets analog meters at power stations and on heavy machinery. Cameras equipped with computer vision technology automatically read oil level indicators, temperature meters, and gas density instruments.
AI vision algorithms utilize color-based segmentation to identify the location of indicator needles and scale markings. These systems operate more quickly and with greater precision than humans, preventing hazardous incidents and costly production disruptions.
2. Cable Spooling
In the oil and gas sector, companies install wirelines for well servicing and reservoir assessment, among other applications. As workers pull the tool assembly from a well, they wind the wireline cable onto a spool. Incorrect spooling may result in severe damage to the cable.
Recent computer vision solutions identify irregularities in spooling using sophisticated data analysis techniques and forecast the cable’s location in real time.
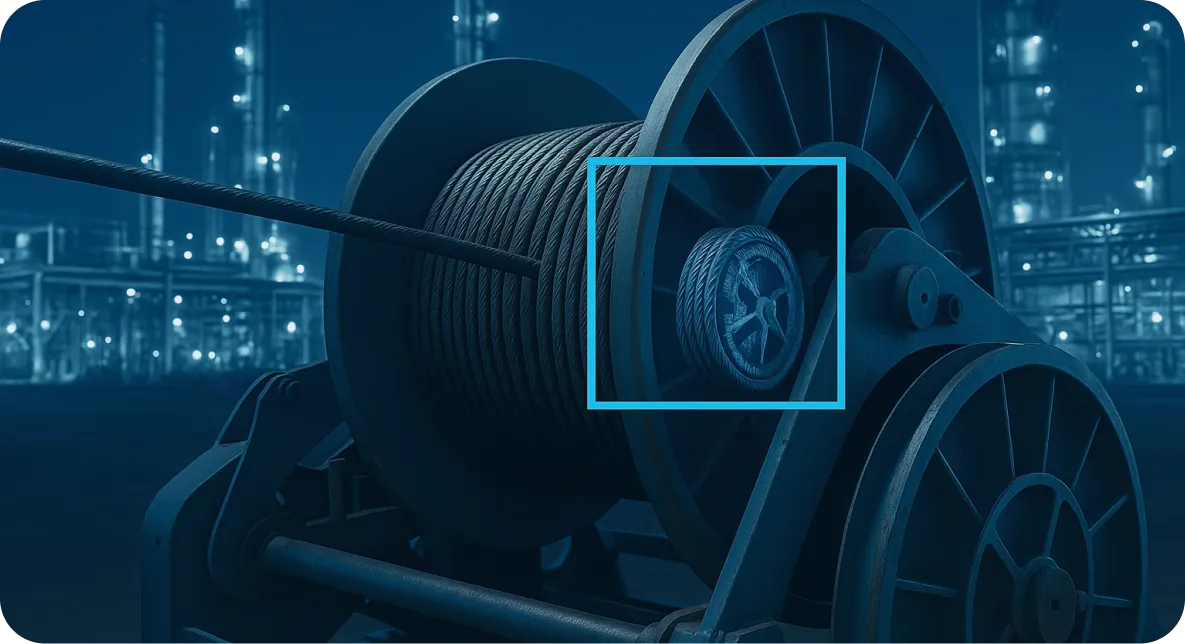
3. Corrosion Detection
Corrosion represents a critical flaw in structural frameworks. It carries considerable financial consequences and can pose a safety threat if not addressed. Workers frequently execute their routine inspection duties in person and under hazardous conditions.
The manual evaluation process proves costly, labor-intensive, and prone to subjectivity. Implementing deep learning techniques to examine camera video footage automates traditional inspection activities.
Corrosion serves as a significant indicator during assessments. Computer vision automates rust identification, resulting in reduced expenses and quicker, more informed decision-making regarding preventive and remedial actions, all supported by large-scale quantitative data.
4. Fingerboard Latch Monitoring
Monitoring the fingerboard latches remains a crucial aspect of maintaining a secure drilling operation and preventing expensive mishaps. Although many rigs already have surveillance cameras to capture footage of the latches, this approach still depends on manual validation of latch positions.
Immediate verification of multiple fingerboards presents a complex, error-susceptible, and high-cost task. When trained to recognize open and closed latch states, computer vision models deliver real-time visual validation of latch status. This technology offers notable cost advantages by reducing the need for human observers while also boosting safety levels.
Computer vision automatically records and analyzes all latch actions for irregularities, reducing risk and strengthening overall rig safety. Through automation, oil and gas firms mitigate operational hazards associated with manual checking errors while streamlining workflow productivity.
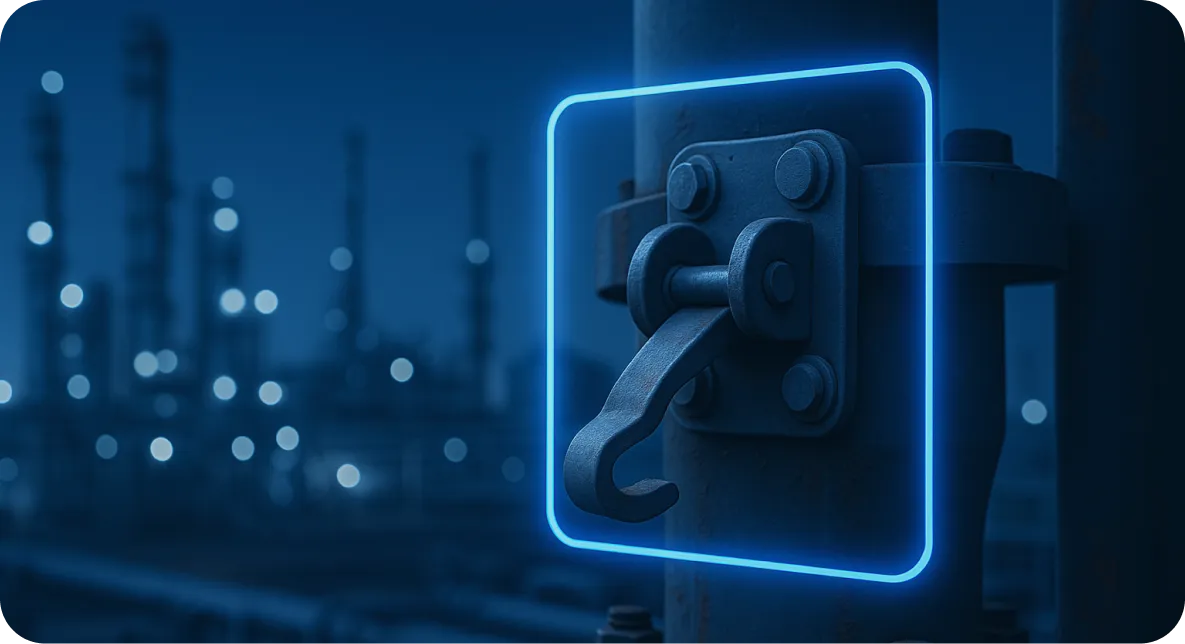
5. Fire Detection
Fires can result in fatalities, significant production downtime, and extensive damage to equipment. Traditionally, human personnel have used surveillance cameras for fire detection, particularly in oil, gas, and chemical plants. However, with hundreds of cameras deployed in large-scale facilities, it becomes nearly unfeasible for human operators to identify fires promptly. Human limitations such as bias, attention lapses, and restricted visual acuity reduce the effectiveness of safety monitoring by manual observers.
Smart fire detection utilizes computer vision techniques with video surveillance to identify fire outbreaks. Certain approaches have demonstrated improved effectiveness by concentrating on smoke identification. These techniques employ background deletion to identify movement and minimize processing demands. Object recognition and image classification algorithms achieve fire detection accuracy of 98.6%, with a 0.15% false alarm rate and an average detection speed of 26.9 milliseconds per frame.
6. Geological Exploration
Computer vision technologies classify rock types using deep neural networks (DNNs) and visual data from rock specimens collected from oil and gas wells. Conventional techniques for petrophysical analysis prove labor-intensive and heavily influenced by the individual expert’s judgment, introducing subjectivity.
In recent experiments, machine learning models achieved an accuracy rate of 93% and were over 900 times quicker than the traditional, manual approach. The research revealed that a second manual evaluation yielded a 92% accuracy rate.
Computer vision in oil and gas is the clear solution for speeding up exploration and eliminating bias in the interpretation process.

7. Leak Detection
Computer vision identifies methane gas leaks using standard infrared imaging devices. For instance, a recent application of deep learning for methane detection streamlined the leak identification process with exceptional precision, reaching accuracy levels between 96% and 98%.
Conventional optical gas imaging (OGI) techniques for identifying methane leaks prove laborious and rely on the interpretation of a human operator to deliver detection outcomes. Computer vision methods for optical gas imaging use convolutional neural networks (CNNs) and training with images of methane emissions to facilitate automated identification.
8. Maintenance Forecasting
In petroleum facilities, deep learning algorithms identify machinery malfunctions and wear. Tailored neural networks train to recognize irregularities during automated inspections of equipment. When an AI system detects a possible problem, an image gets instantly forwarded to a human overseer for further examination.
By consistently tracking machinery performance, computer vision forecasts possible malfunctions, enabling preventive maintenance to reduce operational interruptions and avoid incidents.
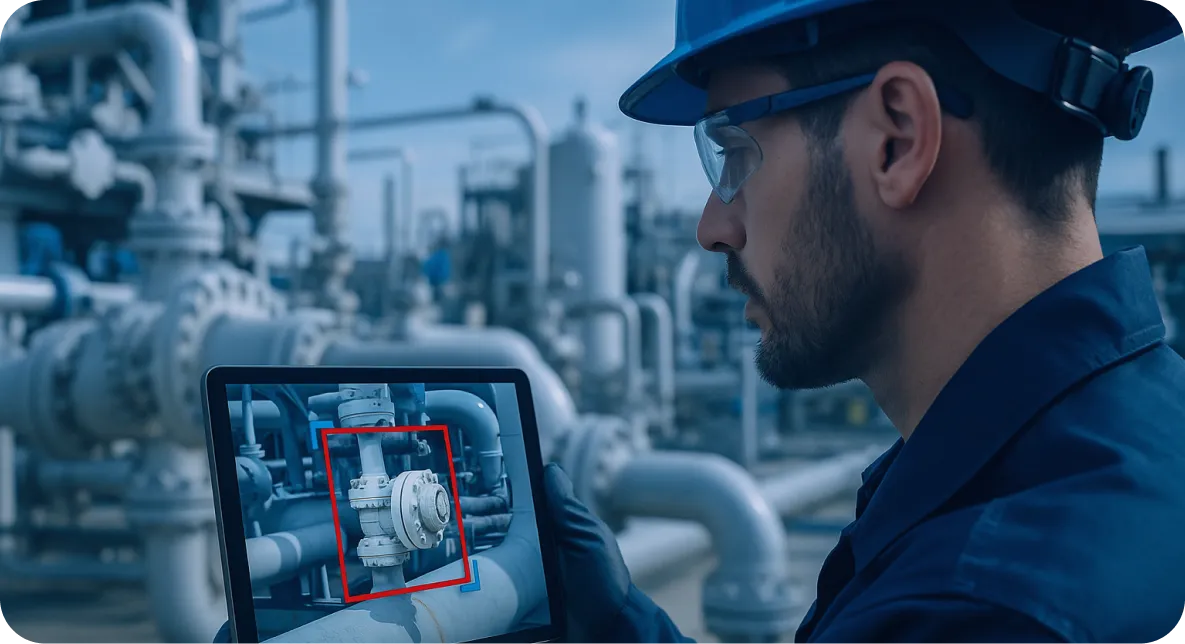
9. Monitoring of Remote Oil and Gas Fields
Live monitoring of oil and gas fields using cameras automates and digitizes oil production areas, particularly for offshore oil and gas operations. These systems boost oil and gas output by observing and forecasting the status of load pumps through machine learning methods.
AI in oil and gas is propelled by affordable sensors and advanced computing capabilities using distributed architectures to derive valuable insights from massive datasets directly at the point of data generation. The broad utility and relatively low expense of cameras enable extensive video analysis without requiring the installation of physical sensing devices.
10. Oil and Gas Pipeline Inspections
Evaluating the state and integrity of extensive infrastructure networks during regular operation and under hazardous conditions presents significant difficulties for operators. Deep learning techniques utilize computer vision algorithms to evaluate the condition of large-scale structures by extracting essential insights from camera-based remote sensing data.
Initially, the images must undergo pre-processing at the pixel level using conventional computer vision techniques. Subsequently, deep learning architectures can assess the status of various essential components. Practical trials have shown that deep learning models can swiftly and precisely identify the location and severity of damage. There is significant potential for large-scale evaluation of oil and gas pipelines across spatial and temporal dimensions compared to traditional approaches.
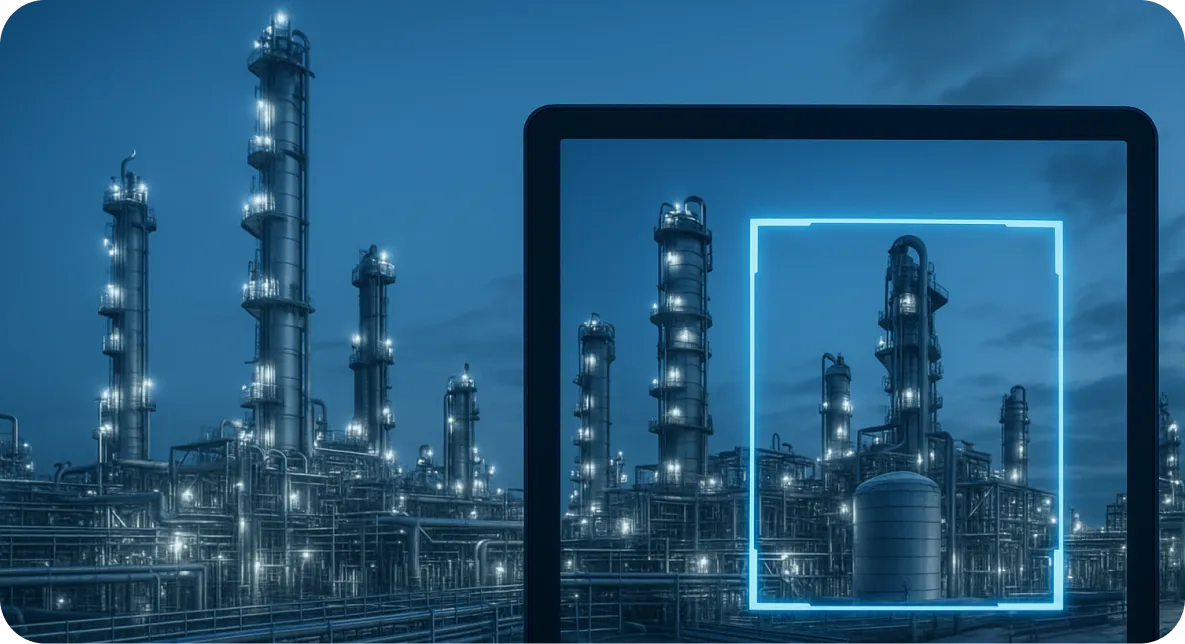
11. Red Zone Integrations
Drilling activities remain complex, involving numerous personnel operating near hazardous equipment. Drill floors often feature designated red zones, where workers must stay vigilant for potential hazards while performing their tasks.
Machine learning algorithms, combined with computer vision, enable real-time monitoring of both machinery and staff, allowing for the immediate detection of intrusions or risky behaviors. If an unauthorized employee enters a prohibited zone or if equipment operates beyond safe limits, computer vision solutions can immediately activate alerts and notify supervisors, enabling prompt intervention to prevent incidents.
Automated surveillance of red zones improves on-site safety, lowering the risk of harm and avoiding expensive interruptions caused by accidents.
12. Workplace Security
Security concerns, like unauthorized access, can be continuously monitored at unmanned operational locations using computer vision technologies, which can instantly alert appropriate personnel. Automated monitoring bolsters protection while lessening the workload on human staff, enabling round-the-clock threat management in high-risk settings.
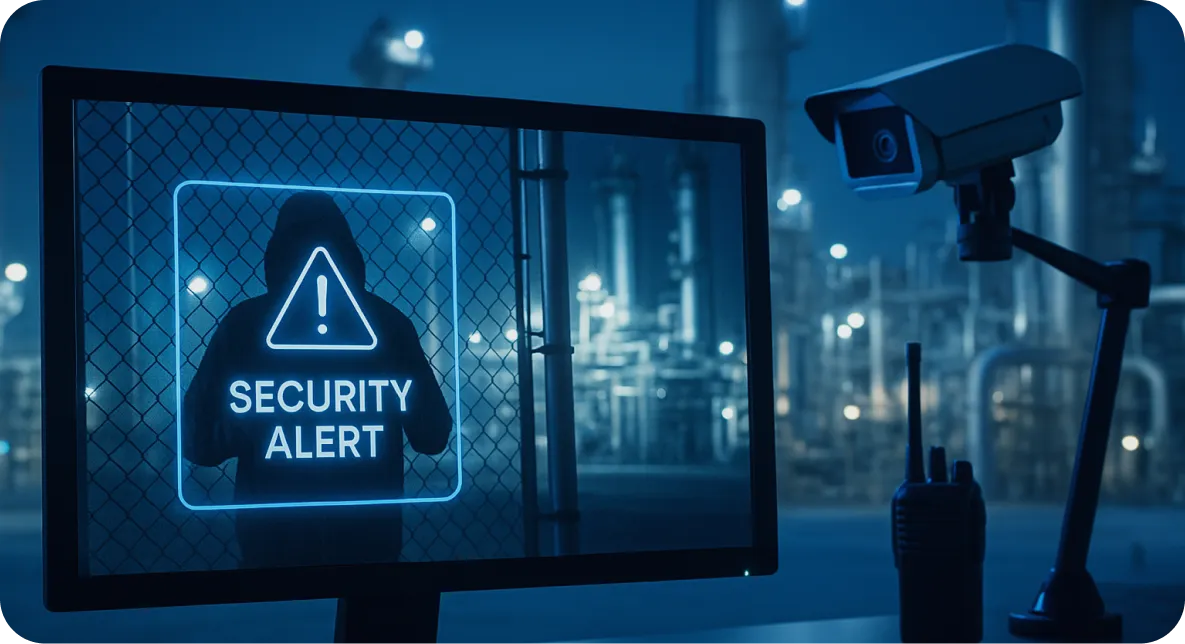
Optimize Oil and Gas Production With the Edge Vision AI Platform
The oil and gas sector is undergoing significant changes due to the adoption of computer vision technologies. Implementing edge AI solutions is essential to fully leverage the capabilities of this innovation. The rapid processing, increased security, and real-time intelligence offered by edge computing make it a vital resource for various applications within the industry. For a free demonstration of the Edge Vision AI Platform and all of its features, request a demo online or call AiFA Labs at (469) 864-6370.